Project
Fielding Wastewater Treatment Plant
Case study
Reliant Solutions shines in challenging Plains Treated Water scheme expansion.
Project brief:
Reliant Solutions completed the full package, we did the earthworks, foundation, tank construction and commissioning.
The tank is insulated.
Designed to capture and store the methane gas given off during the digestion of wastewater.
Story:
The Feilding WWTP is equipped with two digesters (approx. 1,650m3 and 500m3) in series, built in 1967. The second digester is acting as a sludge consolidating tank. The process includes a boiler, a heat exchanger and a gas holder (approx. 17m3).
The ultimate objectives of the Council around the digester project are as follows:
- Increase digestion capacity. With projected potential loads, the optimum digester capacity would be of approx. 5,000m3.
- Be able to treat additional commercial effluents from a number of trade waste customers.
- Increase the production of biogas. A two-stage anaerobic digestion process is considered to optimise the production of biogas.
- Introduce cogeneration to heat the digester and to produce electricity for the treatment plant needs.
- Turn the digested material into compost. The existing system will need to be inspected and refurbished accordingly.
- A new digester tank is required to be able to take off the existing system (step 1).
The inspection will then dictate if refurbishment of the existing equipment or replacement of the first train is the best option (step 2). The benefits of a cogeneration system will be investigated.
The current volume of biogas produced per day is estimated at 550m3/day. Town inflow consumption is on average of 250m3 gas/day. With the characteristics of the current influent, the volume of biogas produced can be increased to more than 1,500m3/day if the feeding regime is optimized. When considering future increase of loadings to the treatment plant (new industrial customers) and increase of digestion volume, the biogas production was estimated to up to 5,800m3/day.
The new digester tank will be located at the Feilding Wastewater Treatment Plant, Kawakawa Rd, Feilding, New-Zealand. The area available for the new anaerobic digestion facility is of 30x42m, next to the existing digester tanks.
From MDC.govt.nz
- The Feilding wastewater scheme is the largest in the District and serves a number of large industries as well as more than 14,000 residents.
Parts of the Feilding wastewater network date back to 1905. The Feilding wastewater treatment plant (WWTP), located on Kawakawa Road to the south of Feilding, was built in 1967. Prior to this plant being built, wastewater was treated in a large septic tank.
The treatment plant has been upgraded over the years in response to increasing domestic/industrial demand and more stringent environmental standards. Significant reductions of loads discharged to the river have already been achieved: DRP (99%), E.coli (98%), CBOD5 (35%) and suspended solids (70%). Remaining upgrade works will target further significant reductions in SIN (ammonia and nitrate N) and optimisation of irrigation to maximise land application.
Currently, the WWTP includes key process elements such as screening, anaerobic and aerated lagoons, sedimentation, clarification and UV disinfection. The existing sludge stream from the sedimentation basins is processed by digestion prior to thickening and stabilisation via storage in sludge lagoons.
New resource consents have been granted and the Manawatu District Council will dispose of a significant proportion of treated effluent from the WWTP onto land. When discharge to land is not possible, treated wastewater is stored (two storage ponds with a total capacity of 25,000 m3 have been constructed). The last option would be to discharge to the Oroua River.
The shift to land disposal will also underpin Council’s commitment to the Manawatu River Accord and local iwi by removing a significant volume of treated effluent which is currently discharged into the Oroua River.
Several major projects are underway to increase the treatment capacity and to create a more robust treatment system. Those include a receiving facility to separate industrial streams from the main treatment processes and to be treated directly in the digester (also being upgraded), sludge dewatering equipment, irrigation system, composting or improved clarification and DRP removal.
Background about our system:
Anaerobic digestion is the breakdown of organic material in the absence of oxygen. The process is a useful method of treating waste organic materials such as animal manures, food wastes, wastewater treatment sludge and agricultural wastes.
The AD process changes a significant part of the organic carbon into biogas, a useful form of energy as it contains approximately 50-70% methane, depending on the materials fed to the process. The nitrogen in the feed material (this is lost when materials are incinerated, which is the other most common method of energy recovery from organic matter) is converted into ammonia which is a form that is easily taken up by plants when the de-gassed slurry, or digestate, is used as a fertiliser (Ward et al. 2008).
Other benefits include improved handling characteristics and decreased odours. The produced biogas is a much more flexible form of energy than heat or electricity produced by incineration, wind or solar technologies because the gas can be used directly for heat or electricity production to complement periods of low wind or solar energy production or scrubbed to natural gas (NG) standards for utilisation in all methods for which NG is used, including vehicle fuels. Also, scrubbing to NG quality allows for a considerable amount of energy storage in the gas grids of many countries.
Scope of work
Full ground improvement works design and construction.
16.37m Foundation including digging the ring-beam, formwork, steel fixing and concrete pour.
Tank Structure including double membrane roof and exterior insulation and cladding.
External stainless steel pipework and valves.
Access Platform.
Design Specs
Application
Biodigestor Tank
Diameter
15.37m
Height
11.28m
Capacity
2,070m3
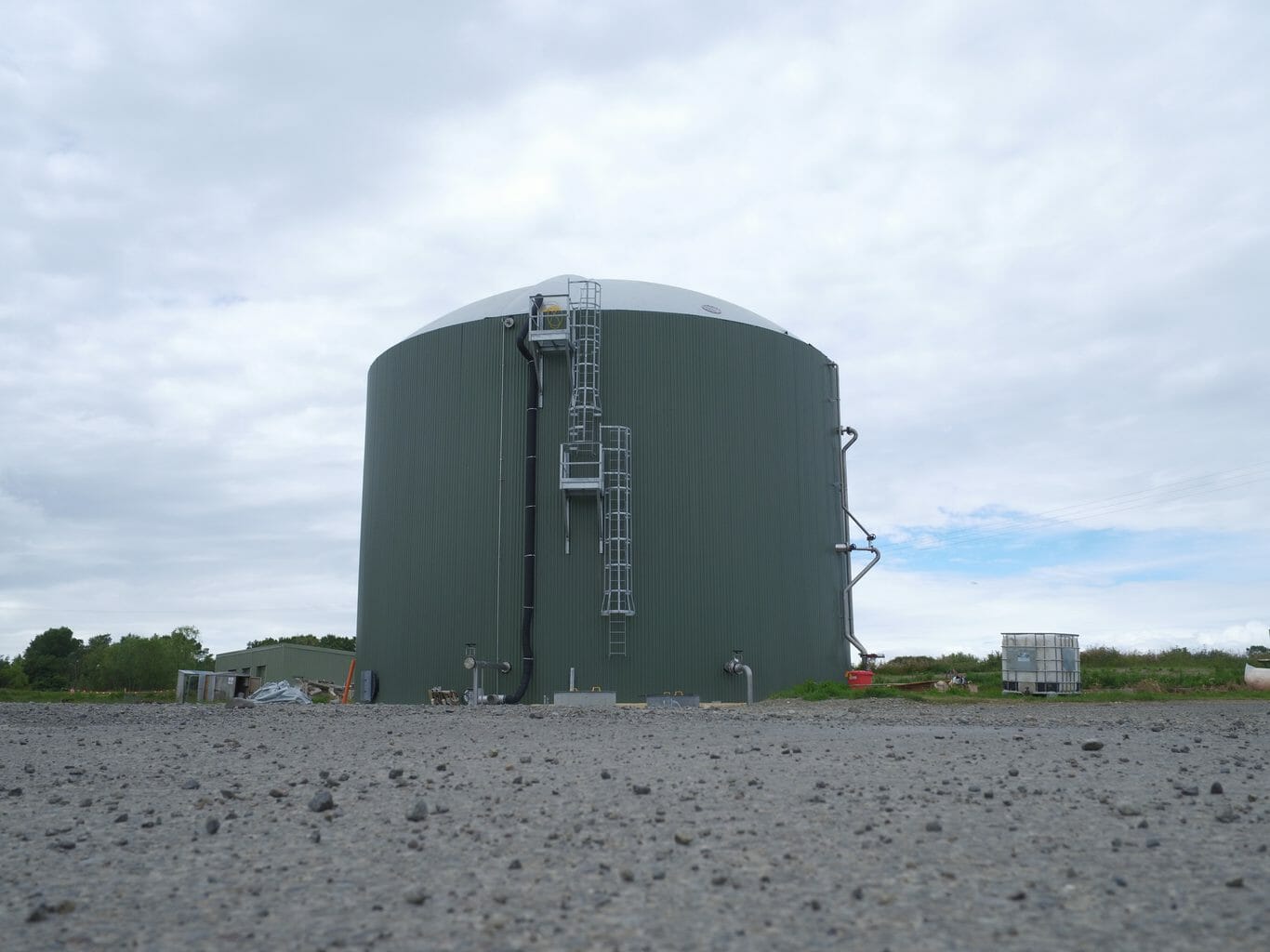
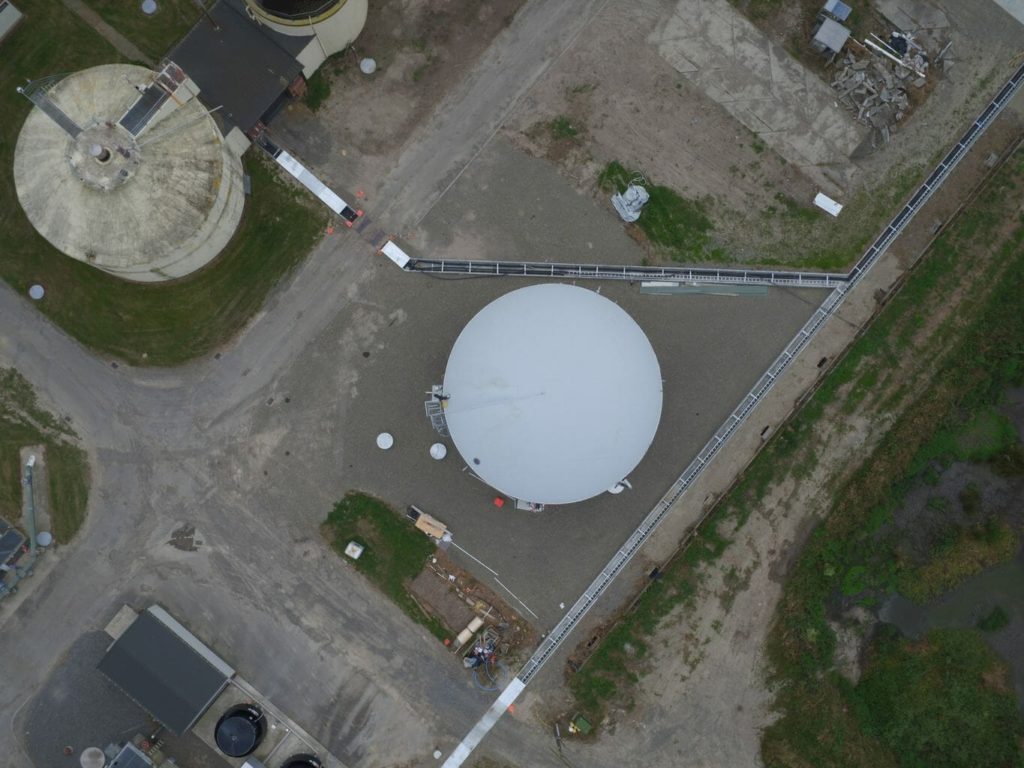
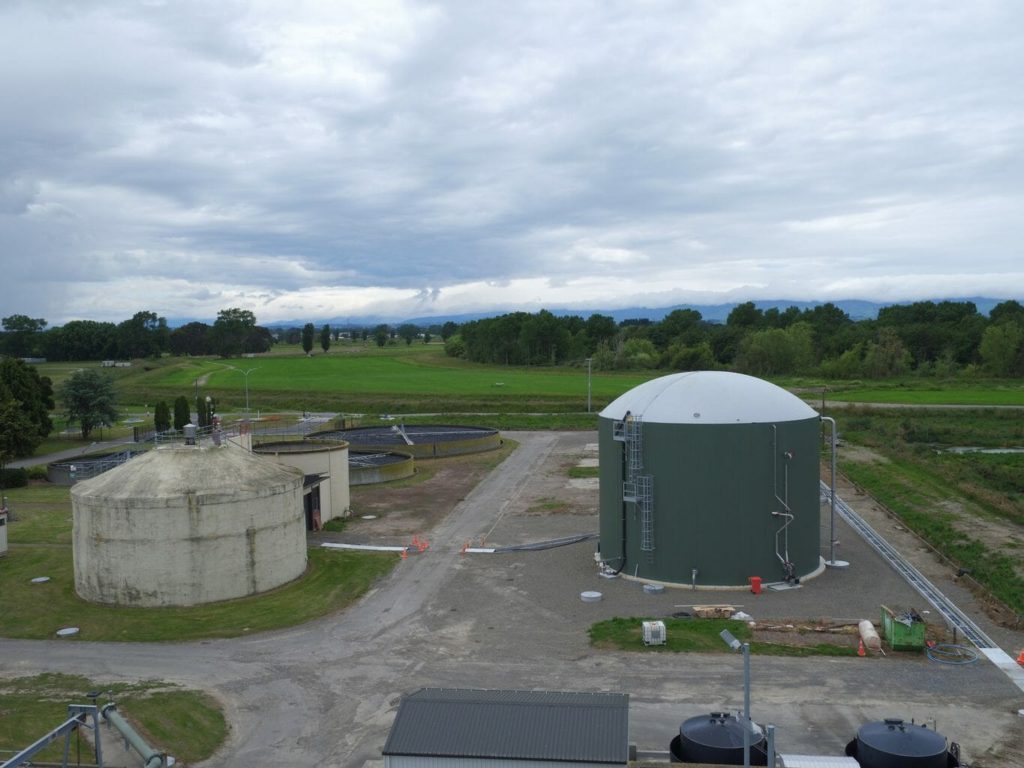
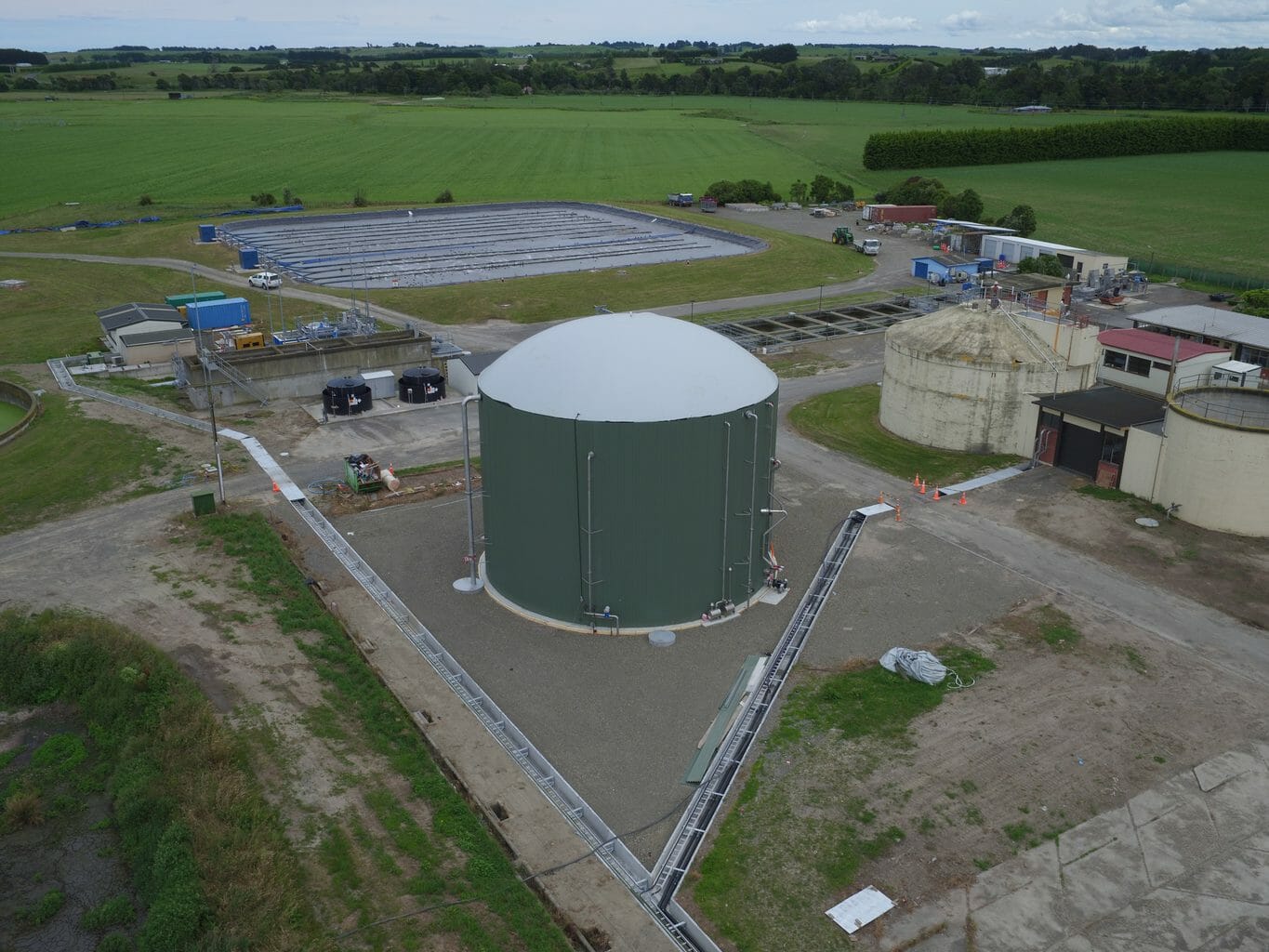